
Steel Scaffolding Design Professional Company Based
China Various Types of Steel Scaffolding Design, Find details about China Steel Scaffolding Design, Bottle Storage Pallet from Various Types of Steel.Five groups of tests were designed to analyze the influence of node types (fastener connection and mortise-and-tenon joint) and reinforcement modes of top horizontal cross rods (weak truss and stiffening truss) on the bearing capacity of the steel tubular scaffold under vertical uniform loads. Embracing the strategy for bucking up our. Is a highly professional company based in Mumbai, and supported by self employed technocrats who design and supply a whole assortment of Steel Scaffolding, Shuttering Material, Steel Spans & Props, Cuplock Scaffolding, Shuttering and Form-work Systems, Components and Accessories using native technology and expertise.
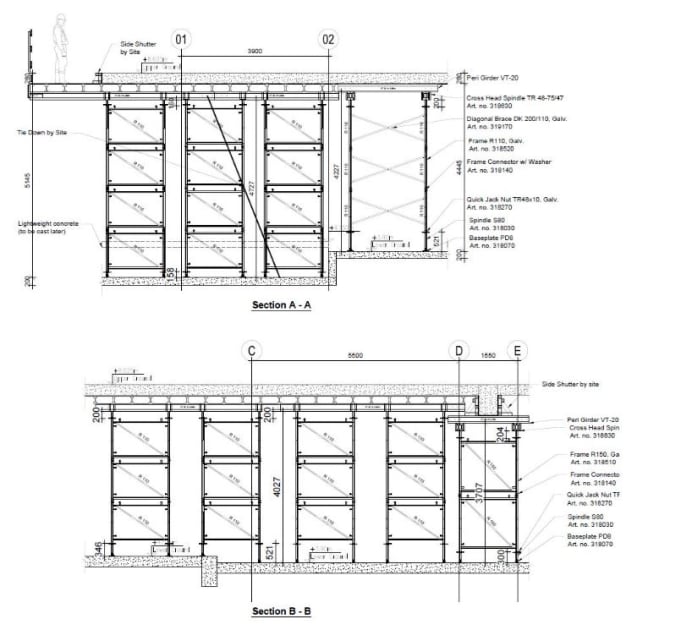
Therefore, research on structural performance and design method of scaffolds has attracted increasing attention from engineering and academic circles.Scaffold design. Nevertheless, frequent and recent collapse and accidents of scaffolds due to improper site management and unreasonable design have resulted in serious economic loss and casualties. The temporary application of scaffolds has led to few studies on its structural performance and design method. At present, common scaffold systems can be divided into fastener, door-type, cuplock-type, access scaffold, and inserting-type steel tubular scaffolds, as shown in Figure 1. Contruction scaffoldingfollows the same pattern with universal & replacable parts.We also specialize in material handling equipment like trolleys and As temporary support structures, scaffolds have been widely applied in engineering construction. Is well known for its nut bolt freeprecision mobile scaffolding based on McMaster USA design.
, Weesner and Jones , and Yu et al. This is attributed to many factors, such as structural defects caused by complicated joint performance, flexible and changeable site installation, repeated use of components, and complicated damage distribution. (e) Inserting-type scaffold.The scaffold is a temporary structure, but its mechanical properties are more complicated than those of permanent steel structures. (c) Cuplock-type scaffold. Because scaffolding must be compatible with a wide array.Pictures of different types of scaffolds. Scaffolding must adhere to OSHA standards for performance requirements and structural design methods.
Godley and Beale , Yue et al. Studied the cuplock-type scaffold by using the probability-based design method. Investigated the load capacities and failure modes of the inserting-type scaffold based on experimental tests supplemented by analyses. The study likewise considered nonlinear materials and the interaction between particular joint elements. Pienko and Blazik-Borowa determined the capacity of the key joint in the inserting-type scaffold based on numerical analysis.
To obtain a safe and stable structural form and scaffold system, a new steel tubular scaffold—mortise-and-tenon steel tubular scaffold—was developed with the Tianjin Xunan Jiahui Building Material Technology Co., Ltd. The present study proposes two types of top-reinforced fastener steel tubular scaffold. Analysis of engineering accidents has revealed that the node joint instability is one of the major causes of scaffold collapse. Failure modes refer to the buckling of vertical rods or defection of top horizontal rods. Cimellaro and Domaneschi comprehensively performed finite element simulations considering the imperfections on three types of steel scaffoldings commonly used in Italy and then proposed an empirical formula to identify the critical load, which has certain reference significance on our research.According to literature review and engineering investigation, failure of steel tubular scaffolds under uniform loads mainly occurs at the top 1-2 layers. Conducted systematic studies on stability capacity and design method of structural steel tubes and coupler scaffolds.
These models are shown in Table 1 and Figures 2– 4. Design of Specimens and Material PropertiesAccording to common construction scaffold structures, five experimental models were designed with comprehensive considerations to scaffold height, vertical and horizontal rod spaces, step distance of rods, height of bottom reinforcing rods, node connection modes, setting of vertical diagonal bracing, and processing methods of top horizontal steel rods. Research conclusions provide technical support for engineering applications and standard specifications of tubular scaffolds. Ultimate bearing capacities and failure modes of the reinforced fastening steel tubular scaffold and mortise-and-tenon steel tubular scaffold under uniform loads were studied through full-size experiments.
Formal loading was calculated according to loads of the whole frame. The preloading included two stages: 3 kN/rod and 6 kN/rod, to assure that the experiment proceeded smoothly. Loading SystemsThe loading process was divided into preloading, formal loading, and unloading.Preloading was performed before formal loading. (1) Counterforce frames (2) hydraulic jacks (3) box-type distribution beams (4) 20a-type joist steels.
Succeeding loading stages continued until strain and displacement developed. Approaching the ultimate bearing capacity of the frame, 75 kN was applied at each load increment and kept for at least 5 min. When the frame developed evident deformation, 150 kN was applied at each load increment and kept for 5 min.
Fastening Steel Tubular Full-Hall ScaffoldFasteners emitted a light slippage sound when the load was increased from 450 kN to 600 kN. Experimental Phenomenon 3.1. (b) C-axis horizontal beam. (a) A-axis horizontal beam. The loading system is shown in Table 3.Layout of strain gauges on horizontal rods in Models 4 and 5. Upon full-frame deformation, data and image were recollected and unloading followed in two stages.

The maximum slippage of top fasteners was 43.5 mm, which was observed at the top of C2. A few top fasteners broke. Evident large wave deflection was developed on the horizontal rods at the top, with a maximum deformation of 50 mm. The buckling deformation of this specimen’s vertical rods at failure was small.
Fastening Steel Tubular Full-Hall Scaffold Reinforced with Top TrussFasteners emitted a light slippage sound when the load was increased from 1200 kN to 1350 kN, and a slight bending of vertical rods was observed. (c) Slippage of fasteners. (b) Failure of top fasteners. (a) Deformation of horizontal rods.
The scaffold generally developed buckling failure. The load was reduced to 1270 kN due to the breakage of one fastener, ending the process. In this process, the entire vertical rods developed evident large wave buckling deformation (Figure 15(a)). A small load reduction occurred when the load was maintained at 1575 kN through load supplementation. The load was increased to 1575 kN, and the overall bending deformation continued to increase.
(c) Fastener failure at top of diagonal bracing. (b) Bending of truss in the loading region. (a) Overall buckling deformation of scaffold. The maximum slippage of the top fastener was 25 mm, which was observed at the top of B5.Failure situations of Model 2.
The loading process ended. The load was reduced while maintaining it at 1425 kN, supplemented upon reduction, and finally stabilized. In the subsequent loading to 1425 kN, the flexural deformation of top horizontal rods increased and the buckling deformation of vertical rods became evident. The deformation sound became louder as the load was increased to 1350 kN, whereas some vertical rods developed bending deformation. The slippage sound became louder when the load was increased to 1200 kN, and flexural deflection of top horizontal rods was observed.
The maximum slippage of top fasteners was 19 mm, which was observed at the top of F4.Failure situations of Model 3.
